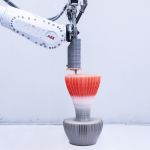
Product design in the digital age according to Nagami
How the Spanish studio wants to revolutionize the entire industry
January 17th, 2022
Never as in recent years has the world of design become the protagonist of the cultural scene. The growing importance attached to aesthetics, the new audience offered to designers by social media and the same growing public interest in the discipline, have redefined an area that, until twenty years ago, remained predominantly niche. It is therefore natural that with this progressive opening of the dialogue with wider worlds, the same design has found itself at the crossroads of new and different areas – digital in the first place. And it is precisely at the confluence of 3D technology, robotics and computational art that Nagami, a Spanish studio founded by Manuel and Miki Jiménez García together with Ignacio Viguera Ochoa, is located. The radical originality in Nigami's production method lies precisely in its use of 3D printing for the production of small and large-scale products, from face masks to the seats and installations exhibited at the Centre Pompidou in Paris, which can not only be customized at will, but which thanks to the many collaborative activities started by the founders have also become a creative medium that has led the singular language of the studio to dialogue with some of the most important voices of contemporary design, art and architecture such as Zaha Hadid Architects, Ross Lovegrove, Daniel Widrig and Davide Quayola.
In 2022 multidisciplinarity is a must, and the intuition behind the work of the Nagami studio was to create, conceptually speaking, a versatile tool that could apply the same aesthetic language not only to different fields, ranging from decorative arts to interior design, to contemporary art up to utilitarian products such as face masks, but also to different creatives having as a unifying element production methods and hybrid visual codes. When we talk about multidisciplinarity we mean not only the ability to devote oneself to projects that are also very different from each other, but also a creative ownership that goes from the concept at the base of the individual designs to the development of software and production. A sort of modern and futuristic version of those Renaissance workshops where the artist himself designed a palace, from the initial drafts of the façade to the choice of individual blocks of marble and the sculpture of all the different elements that made up the final structure.
This freedom to range through different languages lies in Nagami's own methods. As co-founder Manuel Jìmenez Garcia explained in an interview 2018: «Additive manufacturing technologies allow for formal freedoms that would be unattainable with other methods. The type of geometry that our brand promotes would have little viability if we used more traditional technologies, such as injection or blow molding, or even other numerical control technologies». And if much of the design of the traditional product can be described as the practical way of circumventing production limitations, it can be seen how Nagami has changed the paradigm, adapting the production technology according to the singular needs of each product – with the added advantage of avoiding the waste of materials as with 3D printing only the material necessary for the creation of the single product is produced. Despite being very complicated, in fact, the design of the VoxelChair v1.0, which is now part of the permanent collection of the Centre Pompidou, was carried out without smudges or calculation errors but above all without producing waste.
Sustainability is one of the main factors of the studio's work: its extrusion method, perfected by the founders themselves, infinitely compresses the supply chain, cuts initial capital investments on the production of specific molds and machinery or assembly lines, moving from digital design to prototype creation within a few hours, and also speeding up all the testing phases. The production chain so narrow, and which often turns entirely in the same workspace, cuts emissions a lot as well as both in the production phase and in the shipping phase. A type of new work methodology that is already revolutionizing the product design industry and that will soon become its future – a future that Nagami has already anticipated by years.