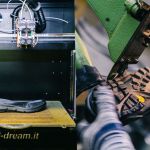
The world in a sole: a journey into the heart of Vibram
We were in the Vibram factory, where the soles of millions of sneakers are born
August 25th, 2021
Filippo D'Asaro
Albizzate is a typical Lombard town between Gallarate and Lake Varese, in the distance you can see the profile of the Alpine arc while driving through the villas and buildings of the center, few could imagine that in via Colombo there is the beating heart of one of the world's leading companies in the footwear industry. With a turnover of over 200 million euros and production plants in China and the USA, Vibram is one of the hidden excellences of Made in Italy: specialized in the production of rubber soles, the importance of Vibram is not only in the numbers (it is estimated that over 50 million soles are produced every year), but above all in the attitude to innovation and research, both technical and aesthetic. The Albizzate plant embodies this company philosophy by keeping together the entire creative and production process of a single sole in the same place: from the drawing tables of the creatives, to the cooking ovens of the soles and passing through the test room of the product.
nss magazine spent a day in the Albizzate plant browsing through machinery, compounds and 3D printers to understand how the best soles in the world are produced.
Vibram's mission is closely linked to its origins and the history of its founder Vitale Bramani, from whom the name of the company derives (VI-tale BRAM-ani). In 1935 Bramani was one of the survivors of a tragedy in the mountains where six mountaineers lost their lives. Blocked by the cold because of the leather and hemp soles, Bramani sensed how rubber was suitable for shoe soles. So, thanks to the collaboration with Pirelli, in 1937 he patented the historic Carrarmato sole, still in production today. The outdoor component has remained one of the main characteristics of Vibram's DNA after almost ninety years, despite the fact that today the market base has also expanded to sectors such as work shoes, casual and high fashion. Today, every Vibram sole - and especially outdoor products - is tested in the control room, where specialized engineers control grip on different surfaces, including an ice rulant. The laboratory analyses are then integrated with the data accumulated on the field by Vibram athletes who test the product on surfaces and environments around the world.
In the next room there is instead the brain of the implant, the space where designers design new soles. Despite the company's core business is outdoors and performance whose soles do not require great aesthetic variation, Vibram has developed in the last various partnerships with streetwear brands for the development of projects on luxury sneakers. Here the Vibram designers work on the client's brief proposing soles that have up to five components, the prototypes are then modeled by a 3D printer to get an idea of the aesthetics of the sole and once the design is confirmed the industrial mold is developed for production. One of the most recent examples of a sole coming out of Albizzate is the collaboration with Alyx, but also Balenciaga which has reinterpreted one of the very few finished products under the Vibram brand: the Vibram FiveFingers. That of finished products remains, however, a side business for Vibram, useful, however, to test - and in some cases create - very interesting market niches: from the barefoot running movement or the wrapping sole of the Vibram Furoshiki winner of the Compasso d'Oro award in 2018, up to the DIY expressants with the Vibram Components.
The creative bulletin board of the designer room shines through as much as the fact that Vibram is at the intersection of various markets, generating a creative wealth and a vision with a potential that few other brands can have.
The last part of the visit to the center of Albizzate takes us to the beating heart of the company: the production plant. After passing the tests of resistance and aesthetics, the compound that will make up the rubber is digested by a huge machine in a process that is very reminiscent of pasta processing. The solid rubber blocks are loaded into the first machine that first kneads them hot and then spreads them immediately after in large canvases that are in turn divided into blocks. These pieces of rubber are inserted by an operator into a mold that returns the soles, subsequently cooked in the process of vulcanization of the rubber aimed at chemically conferring those essentially elastic characteristics, instead of the original plastic ones, in order to increase their wear resistance and softening temperature.
The work of the lines has a strong manual component - in the finishing of the waste for example - and is moving towards the goal of sustainability. As Paolo Manuzzi said in an interview on nss: "Vibram has always believed in sustainability. Ours is an outdoor company, linked to nature and the mountains. It is in our DNA, our company philosophy is based on not damaging nature, on the community of those who love the mountains and the outdoors: if we destroy it, we destroy our future first and then our business." The sustainability that today is often bandied about inappropriately by industries that still have a lot to work on, is a concept that is addressed in a complex and realistic way by Vibram, which continues to invest in sounding and maintenance services in a circular perspective. Just logically following this philosophy, leaving the industrial area you find yourself again in the entrance hall of the center of Albizzate, where memorabilia and historical objects of the brand are exhibited: a material dimension of a history and an industry that perhaps shows too little behind the scenes compared to a virtual and sparkling reality.