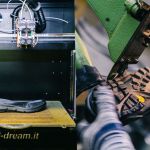
Il mondo in una suola: viaggio nel cuore di Vibram
Siamo stati nello stabilimento di Vibram, dove nascono le suole di milioni di sneaker
25 Agosto 2021
Filippo D'Asaro
Albizzate è un tipico paese lombardo tra Gallarate e il lago di Varese, in lontananza si intravede il profilo dell’arco alpino mentre guidando tra le villette e gli edifici del centro, in pochi potrebbero immaginarsi che in via Colombo si trova il cuore pulsante di una delle aziende leader mondiali dell’industria del footwear. Con un fatturato di oltre 200 milioni di euro e stabilimenti produttivi in Cina e USA, Vibram è una delle eccellenze nascoste del Made in Italy: specializzata nella produzioni di suole di gomma, l’importanza di Vibram non sta solo nei numeri (si stima che vengano prodotte oltre 50 milioni di suole ogni anno), ma soprattutto nell’attitudine all’innovazione e alla ricerca, sia tecnica che estetica. Lo stabilimento di Albizzate racchiude questa filosofia aziendale tenendo insieme tutto il processo creativo e di produzione di una singola suola nello stesso posto: dai tavoli da disegno dei creativi, fino ai forni di cottura delle suole e passando per la test room del prodotto.
nss magazine è trascorso una giornata nello stabilimento di Albizzate curiosando tra macchinari, mescole e stampanti 3D per capire come si producono le suole migliori del mondo.
La mission di Vibram è strettamente legata alle sue origini e alla storia del suo fondatore Vitale Bramani, da cui deriva il nome dell’azienda (VI-tale BRAM-ani). Nel 1935 Bramani fu uno dei superstiti di una tragedia in montagna dove persero la vita sei alpinisti. Bloccati dal freddo a causa delle suole in cuoio e canapa, Bramani intuì come la gomma fosse adatta per le suole delle scarpe. Così, grazie alla collaborazione con la Pirelli, nel 1937 brevettò la storica suola Carrarmato, ancora oggi in produzione. La componente outdoor è rimasta a distanza di quasi novant’anni una delle caratteristiche principali del DNA di Vibram, nonostante oggi il bacino di mercati si sia allargato anche a settori come le scarpe da lavoro, il casual e l’alta moda. Oggi ogni suola Vibram - e in particolare i prodotti per outdoor - viene testata nella control room, dove ingegneri specializzati controllano il grip su diverse superfici, incluso un tapis rulant di ghiaccio. Le analisi di laboratorio vengono poi integrate con i dati accumulati sul campo dagli atleti Vibram che testano il prodotto su superfici e ambienti di tutto il mondo.
Nella sala accanto c’è invece il cervello dell’impianto, lo spazio dove i designer progettano nuove suole. Nonostante il core business dell’azienda sia l’outdoor e la performance le cui suole non richiedono grandi variazione estetiche, Vibram ha sviluppato negli ultimi varie partnership con brand streetwear per lo sviluppo di progetti su sneaker di lusso. Qui i designer Vibram lavorano sul brief del committente proponendo suole che hanno fino a cinque componenti, i prototipi vengono poi modellati da una stampante 3D per avere un’idea dell’estetica della suola e una volta confermato il design vengono sviluppati lo stampo industriale per la produzione. Uno degli esempi più recenti di una suola uscita da Albizzate è la collaborazione con Alyx, ma anche Balenciaga che ha reinterpretato uno dei pochissimi prodotti finiti a marchio Vibram: le Vibram FiveFingers. Quello dei prodotti finiti rimane comunque di un side business per Vibram, utile però per testare - e in alcuni casi creare - delle nicchie di mercato molto interessanti: dal movimento di barefoot running o la wrapping sole delle Vibram Furoshiki vincitrice del premio Compasso d’Oro nel 2018, fino agli esprimenti di DIY con le Vibram Component.
La bacheca creativa della sala designer traspare quanto il fatto che Vibram si trovi all’intersezione di vari mercati, generando una ricchezza creativa e una visione con un potenziale che pochi altri brand possono avere.
L’ultima parte della visita nel centro di Albizzate ci porta nel cuore pulsante dell’azienda: l’impianto produttivo. Dopo aver passato i test di resistenza e di estetica, la mescola che comporrà la gomma viene digerita da un enorme macchinario in un processo che ricorda molto la lavorazione della pasta. I blocchi di gomma solida vengono caricati nel primo macchinario che prima li impasta a caldo e poi li stende subito dopo in grandi tele che vengono a loro volta divise in blocchetti. Questi pezzi di gomma vengono inseriti da un operatore in uno stampo che restituisce le suole, successivamente cotte nel processo di vulcanizzazione della gomma volto a conferire chimicamente quelle caratteristiche essenzialmente elastiche, in luogo di quelle plastiche originarie, in modo da aumentarne la resistenza all'usura e la temperatura di rammollimento.
Il lavoro delle linee ha una forte componente manuale - nella rifinitura dello scarto ad esempio - e si sta muovendo verso l’obiettivo di sostenibilità. Come disse Paolo Manuzzi in un’intervista su nss: “Vibram alla sostenibilità crede da sempre. La nostra è un’azienda outdoor, legata alla natura e alla montagna. È nel nostro DNA, la nostra filosofia aziendale si fonda sul non danneggiare la natura, sulla community di chi ama la montagna e l’aria aperta: se la distruggiamo, distruggiamo prima il nostro futuro e poi il nostro business.” La sostenibilità che oggi viene sbandierata spesso a sproposito da industrie che hanno ancora molto su cui lavorare, è un concetto che viene affrontato in maniera complessa e realista da Vibram, che continua ad investire sui servizi di risuolamento e manutenzione in ottica circolare. Proprio seguendo logicamente questa filosofia, uscendo dall’area industriale ci si ritrova di nuovo nella hall di ingresso del centro di Albizzate, dove sono esposti cimeli e oggetti storici del brand: una dimensione materiale di una storia e di un’industria che forse mostra troppo poco il dietro le quinte rispetto ad una realtà virtuale e scintillante.